Translate
viernes, 23 de agosto de 2019
Graphene polymer composite
Suscribirse a:
Enviar comentarios (Atom)
Entrada destacada
PROYECTO EVACUACIÓN MUNDIAL POR EL COMANDO ASHTAR
SOY IBA OLODUMARE, CONOCIDO POR VOSOTROS COMO VUESTRO DIOS Os digo hijos míos que el final de estos tiempos se aproximan. Ningú...
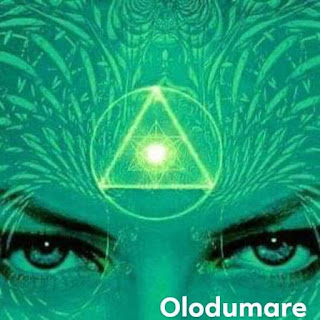
-
Jose Park
-
U.S. Marines arrested disgraced California Governor Gavin Newsom on 1 November, delivering another major blow to the Deep State hegemony’s p...
-
💥💥LA LISTA ES INMENSA!😱😱😱 Los tribunales arrestan a estas personas vestidas de civil. Vimos el arresto de Obama. El arresto se llevó ...
No hay comentarios:
Publicar un comentario
No se admiten comentarios con datos personales como teléfonos, direcciones o publicidad encubierta